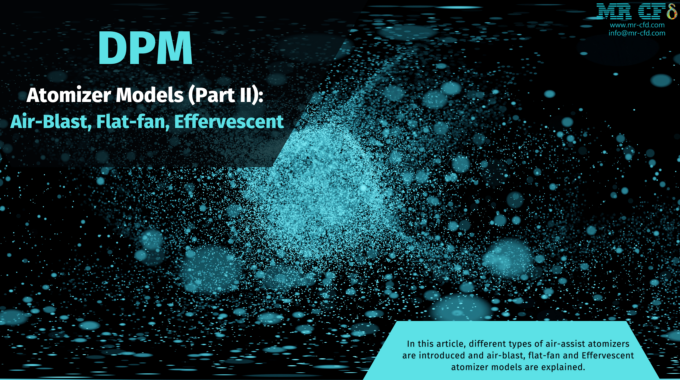
DPM Atomizer Models (Part II): Air-blast, Flat-fan & Effervescent Atomizer Models
Introduction
In this article, different types of air-assist atomizers are introduced and air-blast, flat-fan and Effervescent atomizer models are explained.
Air-Blast/Air-Assisted Atomizer Model
The Fluent Air-Blast / Air-Assisted Atomizer model is a derivative of the Pressure Swirl Atomizer model. An additional air stream is often directed through the atomizer to accelerate the decomposition of liquid sheets. The liquid is converted to a sheet by a nozzle. Then the air is directed to the sheet to increase atomization. This technique is called air-assisted atomization or blast atomization, depending on the air’s amount and velocity. Adding outside airflow to the side of the screen produces smaller droplets than without air.
Although the exact mechanism of this enhanced performance is not fully understood, it is thought that contributing air may accelerate sheet instability. Air may also help disperse the droplets and prevent them from colliding. Air-assisted atomization is used in many similar applications of the Pressure Swirl Atomizer.
As mentioned earlier, the Fluent Air-Blast / Air-Assisted Atomizer is a derivative of the Pressure Swirl Atomizer model. One of the most important differences between the two models is that the thickness of the liquid sheet enters directly into the air blast atomizer model. This input is necessary due to the variety of sheet forming mechanisms used in air blasting atomizers. Therefore, the air blast atomizer model does not use any of the appropriate equations to model the sheet formation used in the rotational compression atomizer model.
Another critical difference is that in the air explosion atomizer model, it is assumed that the breaking of the liquid sheet always occurs due to short waves. This assumption is also since the thickness of the sheet is higher in air explosion atomizers. As a result, the diameter of the ligaments is a linear function of the wavelength of the fastest wave generated on the liquid sheet and is calculated using the following equation:
Where the value of is the ligament coefficient and
its value in Fluent software is equal to 0.5 by default, and Is the wave number corresponding to the maximum growth rate.
Other inputs for this model are the same as the rotational pressure model, among which we can mention the flow rate and flow velocity, which we can see in the following figure of these inputs:
In the air blast model, the atomizer angle is the initial path of the liquid film when leaving the orifice. As you can see, the default value of this angle is 6 degrees.
The length of a ligament fracture is obtained from the following equation:
In this relation is called sheet number, and also Ω is the maximum growth rate; this relation is established for the following condition:
Sheet constant=12(for 2<we<200)
The droplet size is also calculated as follows:
Oh is the Ohnesorge number, which combines the Reynolds and Weber numbers.
Drop velocity is also calculated from the following equation:
where is the velocity coefficient.
Flat-Fan Atomizer Model DPM Spray
A flat fan atomizer injector is very similar to a rotary pressure injector. The difference is that the injection is not liquid; it is done as a flat sheet that is not rotating. This type of liquid injector comes out of a thin and, at the same time, a wide orifice in the form of a flat plate and then decomposes into droplets.
This atomizer’s primary atomization process is the same as the rotary pressure atomizer. Some scientists believe that atomization by a flat fan due to the expansion of the jet in the orifice and the creation of a flat plate is very similar to the atomization of a flat liquid sheet. It is also believed that powdering in the flat fan model can be more than circular orifices.
This model is only used for three-dimensional problems. An image of a three-dimensional flat fan is shown in the first figure. This model assumes that the fan originates from a virtual source. Therefore, it is necessary to determine the location of this origin to determine the intersection of the lines representing the sides of the fan and the arc center from which the fan originates.
Flat fan nozzles
These nozzles stand for high impact and uniform liquid distribution with DPM Spray angles up to 60°. Flat fan nozzles with low flow rates are especially suited for humidifying and spraying. The flow geometry of the nozzle allows the production of accurate, compact sprays available with different distribution patterns.
Nozzle Types
- Low-pressure nozzles
Stable spray angles in a range of pressures. Uniform parabolic distribution and Its shape is as follows:
- High-pressure nozzles
A sharp, uniform flat fan nozzle made from hardened stainless steel and Its figure is as follows:
Adjustable nozzle systems
Ball joint, multi-directional swiveling range of 20°. Simple, quick assembly. Easy adjusting and cleaning. Retains orientation upon replacement.
The breakup of the flat fan is calculated very much like the breakup of the sheet in the pressure-swirl atomizer. The sheet breaks up into ligaments which then form individual droplets. The only difference is that the flat fan sheet is assumed to include ligaments at half-wavelength intervals for short waves. Hence the ligament diameter for short waves is given by
In this case, is taken to be the most probable diameter, with a Rosin-Rammler spread parameter of 3.5 and a default dispersion angle of 6 degrees. The flat-fan atomizer model is like the sheet breakup portion of the pressure-swirl atomizer.
In Ansys Fluent software, we can have any of these inputs as follows:
Effervescent Atomizer DPM Spray
Effervescent atomization Injects a superheated or hot liquid. As the superheated fluid exits the nozzle, it rapidly changes phase. It evaporates, causing the flow to break quickly into small droplets with a wide scattering angle. This injector is used when a boiling liquid is to be drained. In spray combustion, especially in oil furnaces and combustors, effervescent atomizers (twin fluid atomizers with internal mixing) are quickly gaining popularity over more traditional forms of atomization. The DPM Spray formation process in this atomizer does not rely solely on high liquid pressure and aerodynamic forces; instead, a small amount of gas (usually air) is introduced into the liquid before it exits the atomizer a two-phase flow is formed.
When the mixture exits through the nozzle, the pressure drop forces the gas bubbles to expand, causing the liquid to break up. This breakup mechanism allows lower injection pressures and larger nozzle diameters without compromising the drop-size distribution.
In general, the atomization process is divided into primary and secondary breakups. The primary breakup occurs when the fluid flow exits the orifice. Besides being dependent on the properties of the fluids involved, it is also strongly dependent on the atomizer type, its inner structure, and geometry. Secondary atomization is when droplets further break up or collide, leading to various outcomes (reflection, coalescence, breakup, etc.). Unlike primary atomization, secondary atomization depends only on the properties of the atomized liquid (viscosity, velocity, temperature, surface tension, density, etc.) and the surrounding fluid, typically air.
CFD tools have facilitated combustor designs in the last few decades (Jordan et al., 2010; Broukal and Hájek, 2010). For most industrial applications, it is prohibitively expensive to model the two-phase flow inside the atomizer (this would imply using the Euler/Euler approach); therefore, only the Euler/Lagrange approach models external flow. In this case, the gas phase is modeled as a continuum, but the liquid phase is treated as discrete particles (droplets) tracked in the gas flow field. It is, therefore, necessary to use appropriate models for primary and secondary
The initial velocity of the droplets is computed from the conservation of mass, assuming the exiting jet has a cross-sectional area that is times the nozzle area, where is a fixed constant equal to 0.611 as specified in Equation 1.
The maximum droplet diameter is set to the effective diameter of the exiting jet:
The most probable size of the droplet diameter depends on the angle between the random path and the direction of injection, θ (Equation 3). In this relation, The dispersion angle multiplier, θs, is computed from the quality, x, and the specified value for the dispersion constant for the (Equations 4 and 5).
This technique creates a DPM Spray with large droplets in the central core and a shroud of smaller surrounding droplets. The droplet temperature is initialized to 0.99 times the saturation temperature, so the droplet temperature is close to boiling. To complete the model, the flashing vapor must also be included in the calculation. This vapor is part of the continuous phase, not the discrete phase model. You must create an inlet when you specify boundary conditions for the continuous phase at the injection point. When the effervescent atomizer model is selected, you will need to specify the nozzle diameter, mass flow rate, mixture quality, saturation temperature of the volatile substance, spray half-angle, and dispersion constant to specify the position direction of the injector.
The design described in different works can thus be divided into three basic groups, see the following figure:
- Type A: The liquid flows through a central tube in this configuration. Gas is introduced into the liquid by a set of small holes. This “outside-in” gas injection configuration enables a large liquid flow area that prevents clogging. Thus, it is also feasible for the atomization of slurries.
- Type B: Liquid flows through an annular port formed by an atomizer body and aerator tube. Gas is introduced into the liquid in small holes between the aerator side and the bottom. The literature has not found an “inside-out” gas injection modification of the B-type.
- Type C: Both fluids enter separately into the mixing chamber. This configuration enables independent control of the gas and liquid input velocity, direction, and distribution.
you will need to specify the following parameters under Point Properties:
Comments (0)