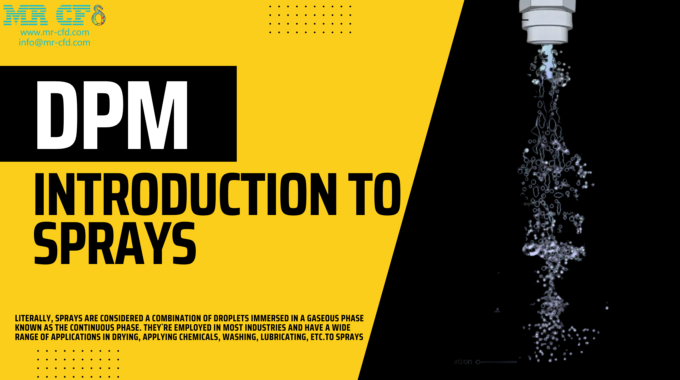
Discrete Phase Model (DPM): Introduction to Sprays
An Introduction to DPM Spray
Literally, sprays are considered a combination of droplets immersed in a gaseous phase known as the continuous phase. They`re employed in most industries and have a wide range of applications in drying, applying chemicals, washing, lubricating, etc. Here are some examples of spray modeling: (for more details, check the links)
Example 1.
In this simulation, a spray drying chamber is simulated. The drying chamber is sprayed with water droplets, and due to the temperature gradient between continuous and discrete phases, heat is transferred to water droplets, and they evaporate. It is a drying application of spraying
Spray Drying Chamber, CFD Simulation Ansys Fluent Software
Figure 1
Example 2.
In this simulation, a gas turbine combustion chamber is simulated. Benzene fuel is injected into the chamber in the form of sprayed particles from the nozzle. It is a chemical applied using a spray.
Combustion Chamber by DPM, CFD Simulation Ansys Fluent Training
Figure 2
DPM Spray: Spray Structure
To better understand spray modeling, we need to delve into spray structure and its characteristics first. In fact, the spraying process can be divided into two main regions.
Figure 3
As shown in figure above, despite fluid dispersion from the beginning of injection due to surface breakups and flow force, the liquid core is retained until primary breakups. After that, the fluid is separated into a mixture of large and small liquid bodies and is still a dense regime but no more liquid core. Just after the occurrence of secondary breakups, the droplets become more uniform and form a dilute regime after a while. So here, we face many challenges and need to consider a wide spectrum of drop sizes, the droplet`s interaction with each other and the continuous phase, phase transition during the process, breakups, and many other parameters that can influence the results.
DPM Spray: Spray Characteristics
Penetration length
One of the prominent characteristics of sprays is penetration length which presents the length from nozzle exit to where the liquid mass beyond that is less than 10% of the total mass in the domain. Notice that, It is wrongly defined as the distance from nozzle exit to the farthest particle in some articles. It is obtained from several observations that the flow length reaches an approximately constant value and fluctuates around it after injection. Thus, it can`t penetrate the continuous phase more due to evaporation and atomization. Moreover, the constant value or the penetration length, in other words, depends on injector geometry, inlet pressure, ambient pressure and temperature, fuel properties, etc.
Breakup length
The spray structure was discussed in the previous part. As it said, the liquid core is retained until the primary breakup despite surface breakups from the beginning. This length is another important characteristic of sprays known as breakup length and directly depends on atomization rate.
Mean drop size
A spray nozzle injects droplets of different sizes that can be summarized in a defined number. There are many definitions for mean diameter measurement, but Ansys Fluent report some of them, including Sauter mean diameter(D32), DV90/DV50, mean diameter(D10), surface diameter(D21), volume diameter(D31), and De Brouckere diameter(D43). Their definition isn`t our concern here and will be introduced later.
Spray Modeling
There are two kinds of approaches to spray modeling: Eulerian & Lagrangian. In the eulerian approach, the software considers droplets and gaseous phases as two continuous phases and solves the governing equations. It can perfectly resolve liquid-gas interface and droplets interactions but needs extremely fine mesh and extra work to consider evaporation. Ansys Fluent suggests a VOF model for this Eulerian approach. From the Lagrangian view, the particles are considered and tracked along with continuous phase, so it perfectly takes evaporation and atomization into account and is a better option to simulate breakups. The discrete phase model (DPM) module is provided in Ansys Fluent for the Lagrangian approach.
For ideal spray modeling, many parameters should be specified accurately. The injector geometry, initial drop size distribution, initial particles velocity, and spray angle are some of these parameters. Several spraying sub-models are provided in Ansys Fluent as well, including breakup model, collision model, evaporation model, etc.
Comments (0)